Episode 6:
Hard times
Leadership under threat and First World War.
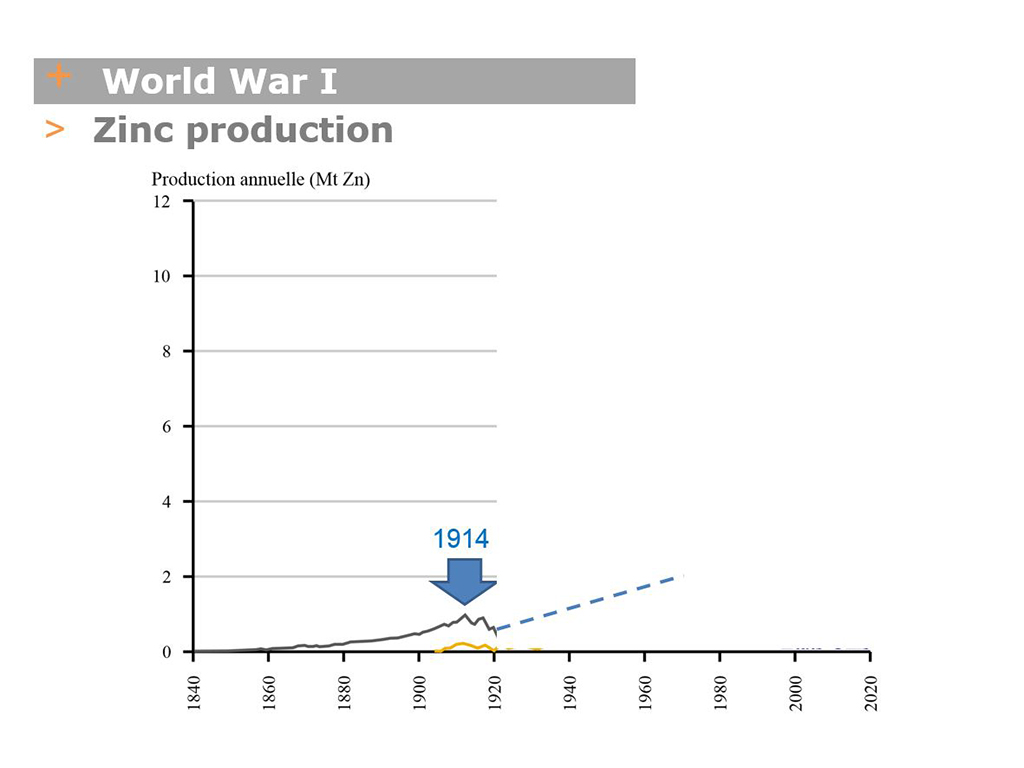
Thanks to economic growth and pertinent industrial choices, the use of zinc underwent rapid growth during the 19th century. Until the 1880s, business was boosted by the almost exclusive use of zinc for roofs and rainwater systems on buildings (see episode 2 & 3, including Haussmannian revolution and great expositions).
Zinc is not just a rolled product!
But new uses emerged which drove the growth of the company. Among these, zinc white (*), which was first produced on a small scale in England in the 1830s, and subsequently was industrially produced in France from 1845 by Vieille Montagne. In the space of just a few years, this highly pure zinc oxide successfully replaced white lead in paints for artists. The Impressionists liked its capacity to remain luminous over time.
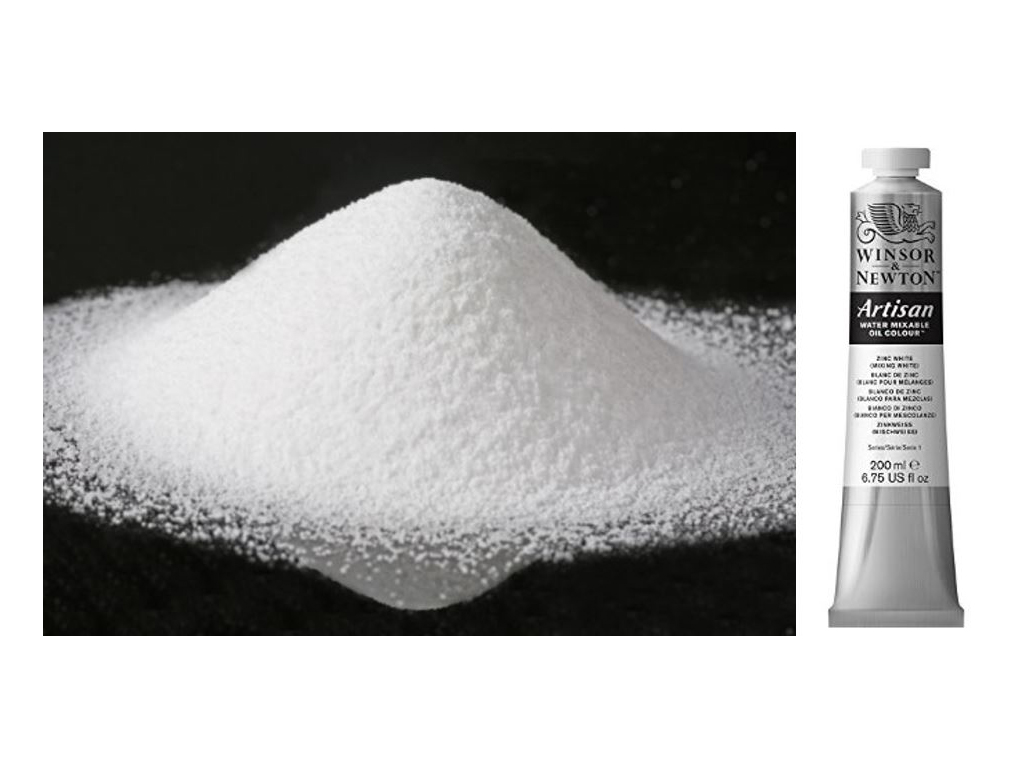
However, the real accelerator for zinc was galvanisation (°), a technique to protect steel using a thin layer of zinc. After a slow start at the end of the 19th century, galvanisation expanded as steel was increasingly used in industry, infrastructures and transport. The famous corrugated metal owes its irresistible success to galvanisation. The latter became the main outlet for zinc prior to the Second World War.
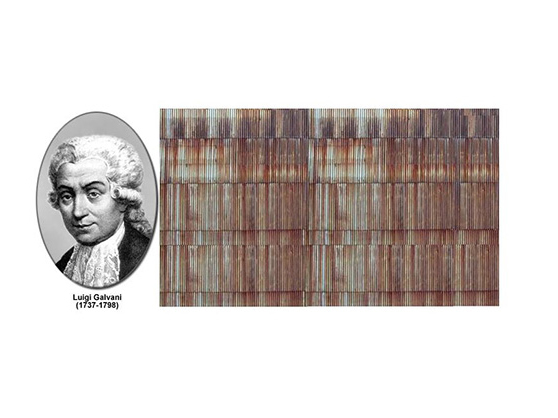
The linear increase in zinc consumption (see PHOTO A: 1830-1914 production curve) obliged Vieille Montagne to search for new mines to supply its Belgian plants with ore. This led to a frenzy of acquisitions that significantly extended the company’s network of sites in Europe (see table of VM sites VM with acquisition dates)
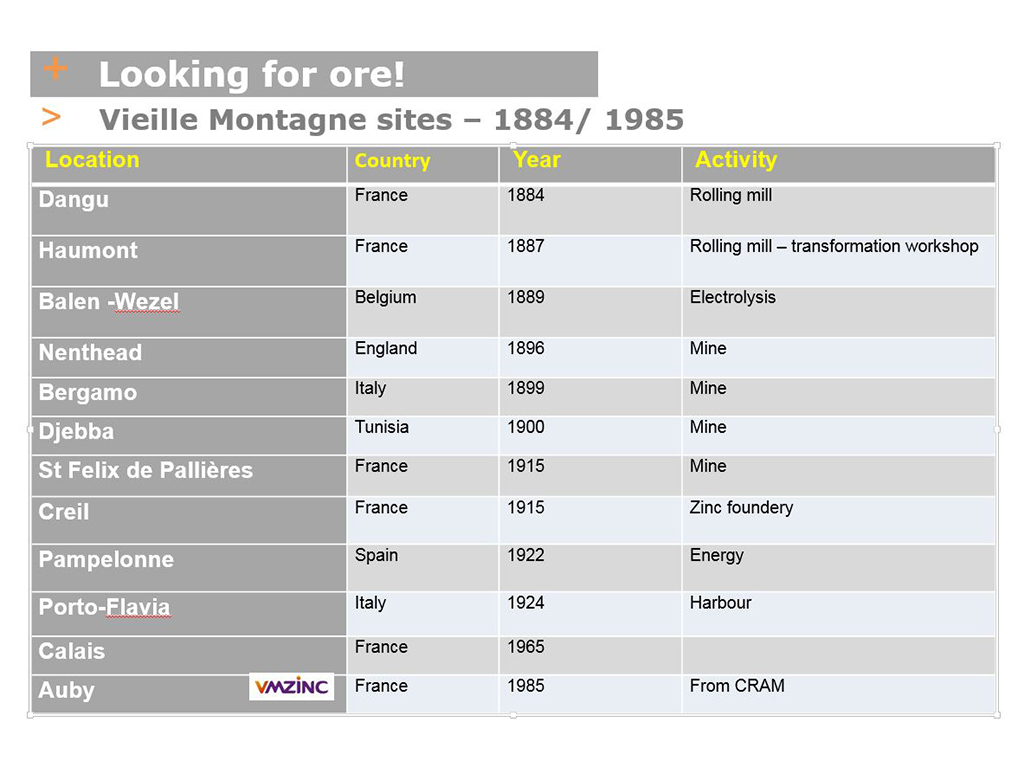
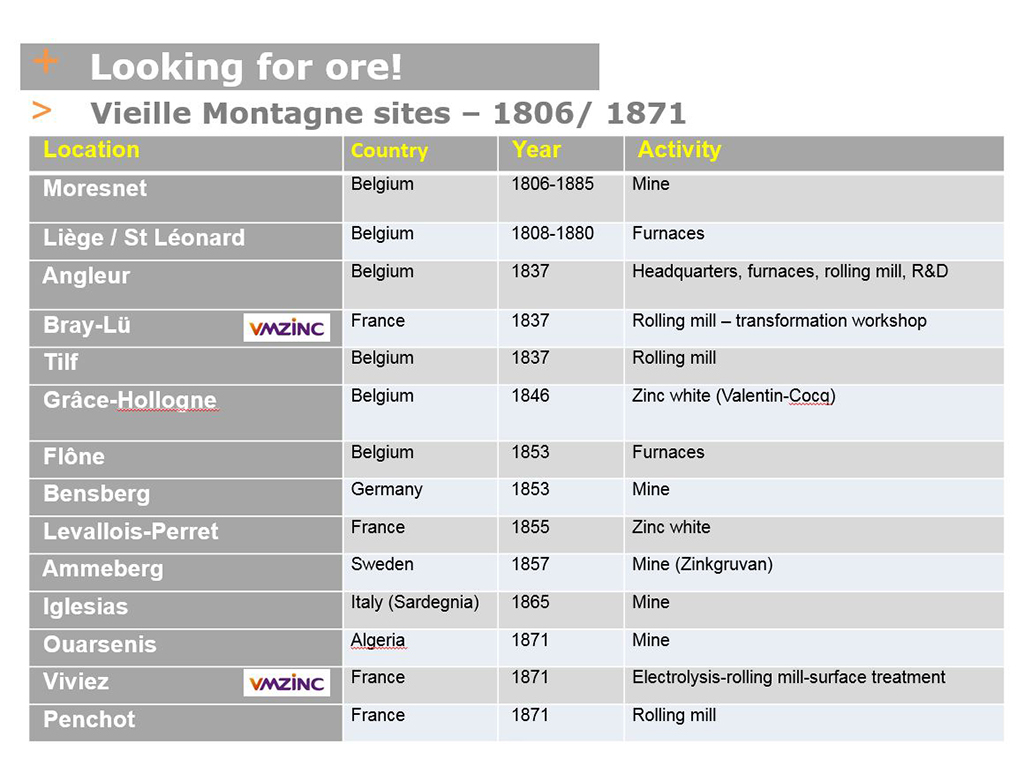
I will have an opportunity to revisit this subject in episode 7, in which I will tell you about my visit to the old Nenthead mine in the UK, which was purchased in 1896.
1887-1913: the leadership of the Belgian zinc industry under threat
This new reality in terms of use and supply profoundly changed the structure of the zinc market. Between 1887 and 1913, six companies working in the non-ferrous sector were set up in Belgium at the initiative of German businessmen. These companies were established close to the port of Antwerp and in the Campine, where they had cheap labour and land. And above all, infrastructures facilitating transport and transit of raw materials by ship. These German firms specialised in the separation of complex ores. They had close links with the large groups that had recently been created in Germany in the sector producing and selling non-ferrous metals: especially Deutsche Gold und Silberscheidestalt (Degussa A.G*) and Metallgesellschaft A.G, set up in Frankfurt 1873 and 1881 respectively.
Other German trading groups collaborated with Belgian companies producing zinc, including Vieille Montagne. They provided them with facilities to procure raw materials, sometimes bought shares in their capital and organised sales of their products. Belgian leadership of the zinc industry was clearly under threat.
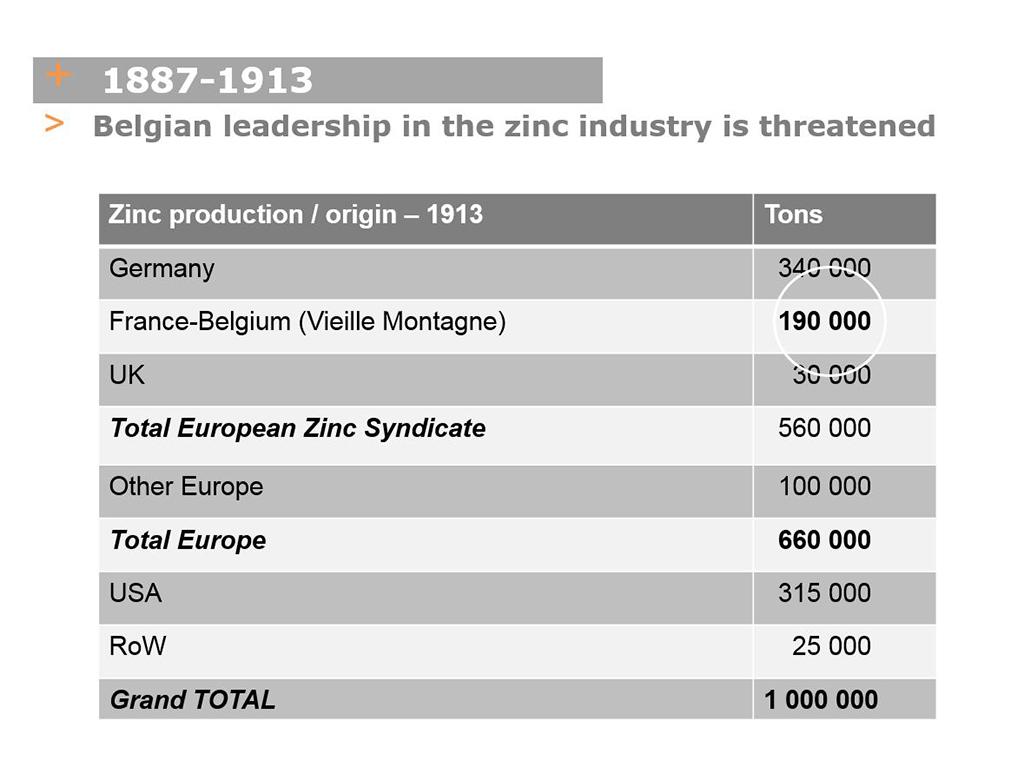
In 1913, the European zinc syndicate controlled overall production of 570,000 tons, of which 350,000 tons (60%) were produced by German producers (including their Belgian subsidiaries), 190,000 tons by Franco-Belgian producers and 30,000 tons by an English group. At the time, worldwide production was already at one million tons, with 314,000 tons produced in America! (see table above).
(*) some of whose assets were acquired by Umicore Group in 2003! A little nod to history!
First World War (1914-1918): Vieille Montagne only manufactured when requisitioned…
In 1914, the German mines and plants of Vieille Montagne were placed under the authority of a specific German commissioner. Those located in the occupied territories continued production as long as they had the necessary ore. But they refused to manufacture products that were likely to be used for manufacturing weaponry until the occupier confiscated these plants. They only delivered their production to Germany after they were requisitioned.
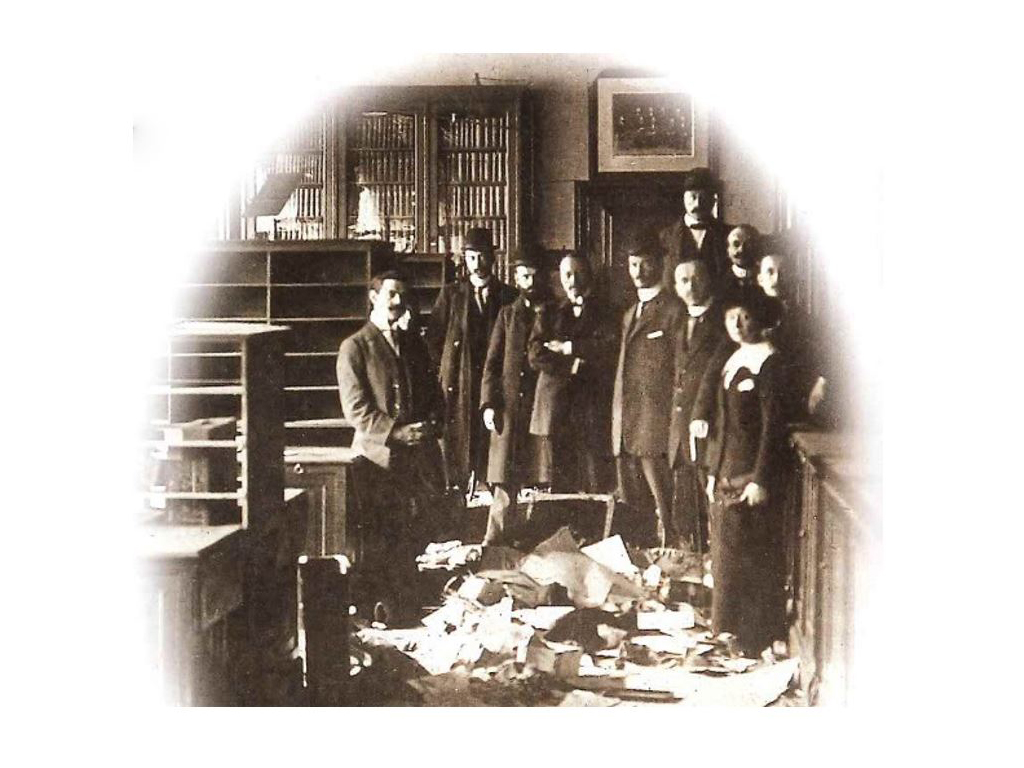
In 1916, after management refused to produce concentrated acid, the Germans immediately took control of the plant in Baelen, Belgium. Another example: in 1917, the German authorities wanted to purchase the mine in Bensberg, Germany, but management at Vieille Montagne courageously refused to enter into negotiations while Belgium was still at war!
(illustration: The Vieille Montagne offices after the visit of the German occupier in October 1914)
… And contributed to the war effort of the Allies
During four years of war, the Germans requisitioned 42,000 tons of zinc, 4,000 tons of lead and 18 tons of silver from Vieille Montagne. However, outside of the occupied zones, the plants belonging to Vieille Montagne, the Compagnie Royale Asturienne des mines and the Union Minière, directed from Paris or London, did all they could to support the war effort of the Allies.
Apart from extra-pure zinc and copper, Union Minière and Vieille Montage supplied many strategic products to the French and English armies, such as iron antimoniate to manufacture shrapnel, acid to produce explosives or zinc oxide to produce tyres for vehicles.
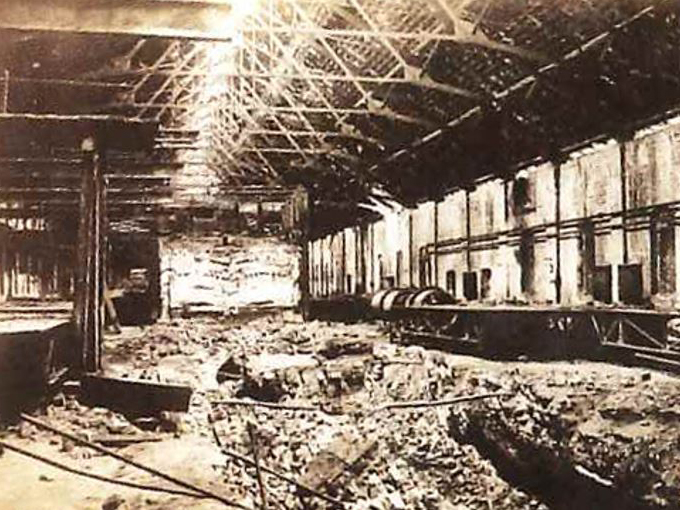
Epilogue
When Germany’s defeat became inevitable, the occupier systematically emptied and demolished certain plants in France and Belgium, such as the plant in Auby, France, belonging to Asturienne des Mines and those in Balen, Belgium and Haumont, France, belonging to Vieille Montagne.
Despite these destructions and thanks to military requirements, this war gave an extraordinary boost to the non-ferrous sector in Europe.
In our next episodes, we will see how zinc consumption continued to increase in the first half of the 20th century and how, thanks to innovation, Vieille Montagne continued to significantly influence this industry.
(*) definition of zinc white
Characterised by the chemical formula ZnO, zinc oxide is water-insoluble. This amphoteric oxide is soluble in basic or acid solutions. It takes the appearance of a whitish powder called zinc white. Zinc oxide is used in many applications, particularly for the manufacture of paints, glass and ceramic. It can also be used as an ingredient in certain sun creams and certain food products.
(°) definition of galvanisation
Galvanisation consists of covering a piece of metal with a thin layer of zinc in order to protect it from corrosion. The treatment is referred to as anti-corrosive. The name comes from the inventor Luigi Galvani (1737-1798), an Italian physician who discovered galvanism.